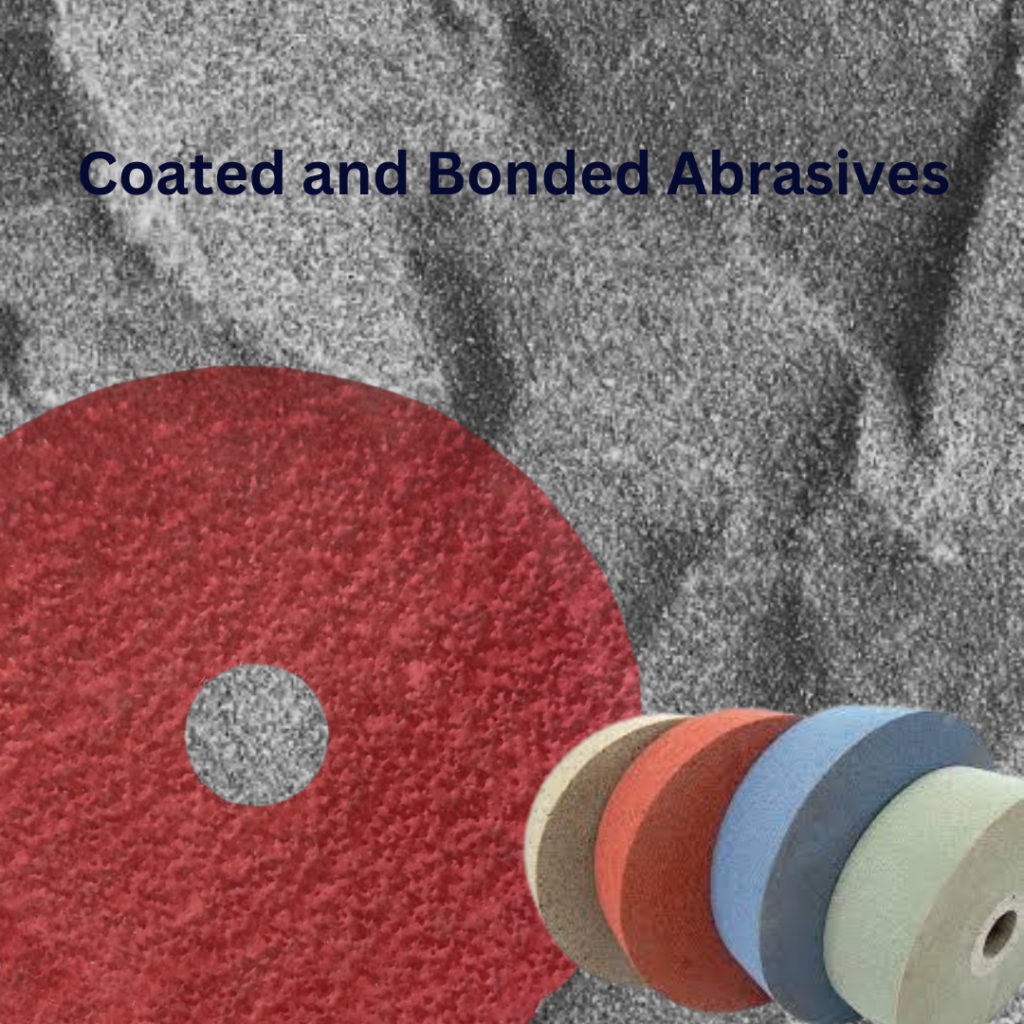
Abrasives play a crucial role in various industries, from metalworking and woodworking to automotive and construction. They are essential tools for shaping, finishing, and polishing surfaces, ensuring that the final product meets the required specifications. Among the various types of abrasives available, coated and bonded abrasives are the most commonly used. Understanding the differences between these two types of abrasives is key to selecting the right product for your specific application.
In this blog, we will delve into the fundamental differences between coated and bonded abrasives, exploring their composition, uses, advantages, and disadvantages. We will also provide insights on how to choose between these two types of abrasives based on your specific needs.
What Are Coated Abrasives?
Coated abrasives are made by bonding abrasive grains to a flexible substrate, typically paper, cloth, or polyester film, using a resin or glue. These abrasives are available in various forms, including belts, discs, sheets, and rolls. The most common example of a coated abrasive is sandpaper.
Composition and Structure
Coated abrasives consist of three main components:
- Abrasive Grains: The abrasive grains are the cutting agents responsible for removing material from the workpiece. Common materials used for abrasive grains include aluminum oxide, silicon carbide, zirconia alumina, and ceramic.
- Backing Material: The backing material provides support and stability to the abrasive grains. It is typically made of paper, cloth, or a polyester film, depending on the application. The choice of backing material affects the flexibility, durability, and overall performance of the abrasive.
- Bonding Agent: The bonding agent is the adhesive that holds the abrasive grains onto the backing material. Resins are commonly used as bonding agents due to their strength and durability. The bond is crucial for determining the life and performance of the abrasive.
Applications of Coated Abrasives
Coated abrasives are versatile and used in a wide range of applications, including:
- Woodworking: Coated abrasives are widely used in woodworking for tasks such as sanding, shaping, and finishing wood surfaces. They are particularly effective for achieving smooth finishes and preparing surfaces for painting or staining.
- Metalworking: In metalworking, coated abrasives are used for deburring, surface preparation, and finishing metal parts. They are also employed in grinding operations where precision and fine finishes are required.
- Automotive: Coated abrasives are used in the automotive industry for sanding and finishing body panels, preparing surfaces for painting, and polishing.
- Construction: In construction, coated abrasives are used for smoothing and finishing drywall, sanding floors, and preparing surfaces for coatings or adhesives.
Advantages of Coated Abrasives
- Flexibility: Coated abrasives are highly flexible, allowing them to conform to the shape of the workpiece. This makes them ideal for sanding curved or irregular surfaces.
- Versatility: Coated abrasives are available in a wide range of grit sizes, making them suitable for various applications, from coarse sanding to fine polishing.
- Ease of Use: Coated abrasives are easy to handle and use, making them suitable for both manual and machine operations.
Disadvantages of Coated Abrasives
- Limited Durability: Coated abrasives may wear out more quickly than bonded abrasives, especially in heavy-duty applications.
- Heat Sensitivity: Coated abrasives can generate heat during use, which may lead to clogging or burning of the workpiece.
What Are Bonded Abrasives?
Bonded abrasives are made by mixing abrasive grains with a bonding material, such as resin, rubber, or vitrified (glass) material, and then forming the mixture into various shapes, such as wheels, discs, or blocks. The most common example of a bonded abrasive is a grinding wheel.
Composition and Structure
Bonded abrasives consist of three main components:
- Abrasive Grains: The abrasive grains are the cutting agents that remove material from the workpiece. Common materials used for abrasive grains in bonded abrasives include aluminum oxide, silicon carbide, diamond, and cubic boron nitride (CBN).
- Bonding Material: The bonding material holds the abrasive grains together in a solid form. The type of bonding material used affects the strength, hardness, and performance of the abrasive. Typical bonding agents consist of resin, rubber, and vitrified materials.
- Reinforcement: In some bonded abrasives, reinforcement materials, such as fiberglass, are added to provide additional strength and stability.
Applications of Bonded Abrasives
Bonded abrasives are used in various heavy-duty applications, including:
- Grinding: Bonded abrasives are widely used in grinding operations, where they remove material from the workpiece through abrasive action. They are essential in manufacturing processes for sharpening tools, shaping metal parts, and finishing surfaces.
- Cutting: Bonded abrasive cutting wheels are used for cutting metal, concrete, stone, and other hard materials. They are commonly used in construction, metal fabrication, and masonry work.
- Polishing: Bonded abrasives are used in polishing operations to achieve smooth and shiny finishes on metal, glass, and stone surfaces.
Advantages of Bonded Abrasives
- Durability: Bonded abrasives are known for their durability and long life, making them suitable for heavy-duty applications.
- Precision: Bonded abrasives offer high precision in material removal, making them ideal for tasks that require tight tolerances and fine finishes.
- Strength: The bonding material in bonded abrasives provides strength and stability, allowing them to withstand high pressure and demanding conditions.
Disadvantages of Bonded Abrasives
- Limited Flexibility: Bonded abrasives are rigid and may not conform well to irregular or curved surfaces.
- Potential for Breakage: Bonded abrasives, especially those with vitrified bonds, can be brittle and may break if subjected to excessive force or impact.
Coated vs. Bonded Abrasives: A Comparison
Now that we have a clear understanding of what coated and bonded abrasives are, let’s compare these two types of abrasives based on several key factors:
1. Material Removal Rate
- Coated Abrasives: Coated abrasives generally have a lower material removal rate compared to bonded abrasives. They are best suited for tasks that require light to moderate material removal, such as sanding and finishing.
- Bonded Abrasives: Bonded abrasives have a higher material removal rate, making them ideal for heavy-duty grinding and cutting applications. These abrasives are capable of rapidly and effectively removing substantial amounts of material.
2. Surface Finish
- Coated Abrasives: Coated abrasives are designed to provide smooth and even surface finishes. They are ideal for tasks that require fine finishing and polishing.
- Bonded Abrasives: Bonded abrasives are more suitable for rough grinding and cutting, where the primary goal is material removal rather than achieving a fine surface finish.
3. Flexibility
- Coated Abrasives: Coated abrasives are highly flexible, allowing them to conform to the shape of the workpiece. This makes them suitable for sanding curved or irregular surfaces.
- Bonded Abrasives: Bonded abrasives are rigid and do not offer the same level of flexibility as coated abrasives. They are best used on flat or uniform surfaces.
4. Durability
- Coated Abrasives: Coated abrasives have a shorter lifespan compared to bonded abrasives, especially in heavy-duty applications. They may wear out quickly and require frequent replacement.
- Bonded Abrasives: Bonded abrasives are more durable and have a longer lifespan, making them suitable for demanding tasks that require consistent performance over time.
5. Cost
- Coated Abrasives: Coated abrasives are generally more affordable and cost-effective for light to moderate applications. They are a good choice for tasks that do not require heavy material removal.
- Bonded Abrasives: Bonded abrasives may have a higher initial cost, but their durability and performance make them cost-effective for heavy-duty applications that require prolonged use.
How to Choose Between Coated and Bonded Abrasives
Choosing between coated and bonded abrasives depends on several factors, including the material you are working with, the type of operation, and the desired finish. Consider these guidelines to assist in making an informed decision:
1. Consider the Material
- Woodworking: For woodworking tasks, coated abrasives are typically the best choice due to their flexibility and ability to provide smooth finishes on wood surfaces.
- Metalworking: In metalworking, the choice between coated and bonded abrasives depends on the specific task. Coated abrasives are ideal for finishing and surface preparation, while bonded abrasives are better for grinding and cutting.
2. Evaluate the Operation
- Sanding and Finishing: For sanding, finishing, and polishing tasks, coated abrasives are the preferred option due to their ability to produce fine finishes and conform to irregular surfaces.
- Grinding and Cutting: For grinding, cutting, and heavy material removal, bonded abrasives are the better choice due to their strength, durability, and high material removal rate.
3. Determine the Desired Finish
- Fine Finish: If achieving a smooth and even finish is your priority, coated abrasives are the best option. These abrasives are engineered to deliver uniform and superior finishes.
- Rough Grinding: If rough grinding and material removal are the primary goals, bonded abrasives are the better choice. They are more effective at removing large amounts of material quickly.
4. Assess the Flexibility Requirements
- Curved or Irregular Surfaces: If you need to work on curved or irregular surfaces, coated abrasives are ideal due to their flexibility. They can easily adapt to the contours of the workpiece, ensuring even sanding or finishing across the entire surface.
- Flat or Uniform Surfaces: For flat or uniform surfaces, bonded abrasives are suitable. Their rigidity ensures stability and precision in grinding or cutting operations.
Conclusion
Choosing between coated and bonded abrasives depends largely on your specific application, the materials you’re working with, and the desired outcome. Coated abrasives excel in tasks requiring flexibility, fine finishing, and versatility, making them ideal for woodworking, surface preparation, and polishing. Bonded abrasives, on the other hand, are the go-to choice for heavy-duty grinding, cutting, and material removal, offering durability, strength, and high precision.
At M/s Sandpaper Rodiez, we understand the importance of selecting the right abrasive for your needs. Our expertise in customizing abrasives to suit specific requirements ensures that you get the perfect product for your project. Whether you need coated abrasives for delicate woodworking or bonded abrasives for tough grinding tasks, we provide high-quality solutions that meet industry standards.
Understanding the differences between coated and bonded abrasives allows you to make informed decisions, optimizing the efficiency and quality of your work. As industries continue to evolve, the need for the right abrasive will remain critical in achieving precision and excellence in various applications. By choosing the appropriate abrasive type and working with a trusted supplier like Sandpaper Rodiez, you can ensure that your operations run smoothly and efficiently, delivering the results you need every time.
For more information or to explore our range of customized abrasives, visit Sandpaper Rodiez. Let us help you find the right abrasive solution for your project today!