
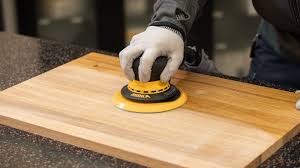

In the world of craftsmanship, whether you’re working on woodworking, metalworking, automotive refinishing, or any other surface finishing project, achieving a flawless finish is often the ultimate goal. The secret to reaching that level of perfection lies in the tools you use, particularly the abrasives. At M/s Sandpaper Rodiez, we understand the importance of using the right abrasive tools tailored to your specific needs. That’s why we specialize in providing customized abrasives that deliver exceptional results, ensuring you achieve the perfect finish every time.
In this comprehensive guide, we’ll explore the importance of choosing the right abrasives, how customized solutions can elevate your work, and share expert surface finishing tips to help you master your craft. Whether you’re a professional or a DIY enthusiast, this blog will provide you with the insights needed to achieve a perfect finish with custom abrasive solutions.
1. Understanding the Role of Abrasives in Surface Finishing
Abrasives are essential tools in any finishing process. They are used to remove material, smooth surfaces, and prepare them for further treatments such as painting, staining, or polishing. The quality of the finish is heavily influenced by the type and quality of abrasive used, as well as the technique applied during the process.
1.1 The Science Behind Surface Finishing
Surface finishing involves the removal of imperfections, scratches, and other surface defects to create a smooth, even, and often shiny finish. This process can involve mechanical methods, chemical treatments, or a combination of the two. Abrasives play a key role in mechanical surface finishing by gradually wearing down the surface to achieve the desired texture and appearance.
1.2 Importance of Using High-Quality Abrasives
Using high-quality abrasives is crucial for achieving consistent and superior finishes. Low-quality abrasives can cause uneven surfaces, scratches, and even damage to the material. At M/s Sandpaper Rodiez, we import the finest sandpaper from around the world and customize it to meet the specific requirements of our clients, ensuring that every project benefits from the best abrasives available.
2. The Benefits of Customized Abrasives
When it comes to achieving the perfect finish, one-size-fits-all solutions often fall short. Customized abrasives offer several advantages over standard options, allowing you to tailor the abrasive to your specific needs and project requirements.
2.1 Tailored to Your Material
Different materials require different abrasive solutions. Whether you’re working with wood, metal, plastic, or glass, the type of abrasive, its grit size, and its backing material all play a critical role in the finishing process. Customized abrasives are specifically designed to work with the material you’re finishing, ensuring optimal performance and results.
2.2 Enhanced Efficiency and Consistency
Using abrasives that are specifically designed for your project can significantly improve efficiency. Customized abrasives allow you to achieve the desired finish with fewer passes, reducing the time and effort required. Additionally, they provide more consistent results across different parts of your project, ensuring a uniform finish.
2.3 Cost-Effectiveness
While customized abrasives may have a higher initial cost, they can save you money in the long run. Their efficiency means you’ll use fewer abrasives and spend less time on each project, reducing overall costs. Moreover, the high-quality finish they produce can increase the value of your work.
3. How to Choose the Right Customized Abrasive for Your Project
Selecting the right abrasive is essential for achieving the perfect finish. Several factors need to be considered, including the material you’re working with, the stage of the finishing process, and the specific finish you’re aiming for.
3.1 Consider the Material
Different materials have different characteristics, and using the wrong abrasive can lead to poor results or even damage. For example:
- Wood: Requires abrasives that can smoothly sand without causing scratches or tear-out.
- Metal: Needs abrasives that can cut through hard surfaces without leaving deep scratches.
- Plastic and Glass: Require fine abrasives that can achieve a smooth, polished finish without causing damage.
3.2 Understand the Stages of Finishing
The finishing process typically involves several stages, each requiring a different type of abrasive:
- Initial Material Removal: Coarse abrasives are used to remove large amounts of material and shape the surface.
- Surface Smoothing: Medium abrasives refine the surface, removing scratches from the initial stage.
- Final Finishing: Fine abrasives are used to achieve a smooth, polished finish, ready for any additional treatments.
3.3 Tailoring the Abrasive to Your Needs
Customized abrasives allow you to tailor the grit size, backing material, and abrasive type to your specific project needs. At M/s Sandpaper Rodiez, we work closely with our clients to understand their requirements and provide abrasives that deliver the best results.
4. Surface Finishing Tips for a Perfect Finish
Achieving a perfect finish requires not only the right tools but also the right techniques. Here are some expert tips to help you make the most of your customized abrasives:
4.1 Use the Right Grit Size for Each Stage
As mentioned earlier, the finishing process involves multiple stages, each requiring a different grit size. Starting with a coarse grit and progressively moving to finer grits will help you achieve a smooth, even finish.
- Coarse Grits (40-60): Use these for initial material removal and shaping.
- Medium Grits (80-120): These are ideal for smoothing the surface and preparing it for finer grits.
- Fine Grits (150-220 and above): Use these for final finishing to achieve a polished, smooth surface.
4.2 Maintain Consistent Pressure
Applying consistent pressure while sanding or grinding is crucial for achieving an even finish. Too much pressure can cause deep scratches or gouges, while too little pressure may not remove enough material. Practice maintaining a steady, even pressure throughout the process.
4.3 Follow the Grain
When working with wood, always sand in the direction of the grain to avoid scratches and achieve a smoother finish. For metals and other materials, follow the natural pattern of the surface for the best results.
4.4 Keep Abrasives Clean and Replace When Necessary
Clogged or worn abrasives can reduce efficiency and lead to poor results. Regularly clean your abrasives to remove dust and debris, and replace them when they become worn to maintain optimal performance.
4.5 Test on a Small Area First
Before starting your project, test your chosen abrasive on a small, inconspicuous area. This will allow you to assess its effectiveness and make any necessary adjustments before working on the entire surface.
5. Common Mistakes to Avoid in Surface Finishing
Even with the right tools, certain mistakes can hinder your ability to achieve the perfect finish. Here are some common pitfalls to avoid:
5.1 Skipping Grit Sizes
Jumping from a coarse grit directly to a fine grit can leave scratches and an uneven finish. Always progress through the grit sizes gradually to ensure a smooth transition between each stage.
5.2 Applying Too Much Pressure
Excessive pressure can cause deep scratches, gouges, and uneven surfaces. Let the abrasive do the work and apply only the necessary pressure to guide it across the surface.
5.3 Using Worn-Out Abrasives
Old, worn-out abrasives lose their effectiveness and can damage the surface. Replace them regularly to ensure consistent performance.
5.4 Ignoring the Material’s Specific Needs
Different materials require different approaches. Using the same technique or abrasive for wood, metal, and plastic can lead to suboptimal results. Customize your approach based on the material you’re working with.
6. The M/s Sandpaper Rodiez Difference: Custom Abrasives for a Perfect Finish
At M/s Sandpaper Rodiez, we pride ourselves on offering high-quality, customized abrasives designed to meet the unique needs of our clients. Our expertise in the industry, combined with our commitment to customer satisfaction, ensures that you receive the best tools for your projects.
6.1 Our Customization Process
We start by understanding your specific requirements, including the material you’re working with, the desired finish, and any unique challenges you face. Based on this information, we tailor our abrasives to match your needs, selecting the right grit size, backing material, and abrasive type for your project.
6.2 Quality You Can Trust
All our abrasives are sourced from leading manufacturers around the world, ensuring the highest quality and performance. Whether you’re working on a small DIY project or a large industrial application, you can trust M/s Sandpaper Rodiez to provide abrasives that deliver exceptional results.
6.3 Serving Clients Across Delhi and NCR, with Plans to Expand
While we currently serve clients in Delhi and NCR, we have ambitious plans to expand our reach across North India and beyond. No matter where you are, you can count on us for reliable, high-quality custom abrasives that help you achieve the perfect finish.
7. Conclusion: Mastering the Art of Surface Finishing
Achieving a perfect finish with customized abrasives is a skill that requires the right tools, knowledge, and technique. By understanding the role of abrasives, choosing the right custom solutions, and following expert finishing tips, you can elevate your craftsmanship and produce exceptional results.
At M/s Sandpaper Rodiez, we’re here to support you every step of the way. Whether you’re a seasoned professional or a hobbyist, our customized abrasives are designed to meet your specific needs and help you achieve the perfect finish. Visit us at Plot No 93, Main Chowk, Samaypur, Delhi – 110042, or explore our range of products on our website at [https://sandpaperrodiez.com]