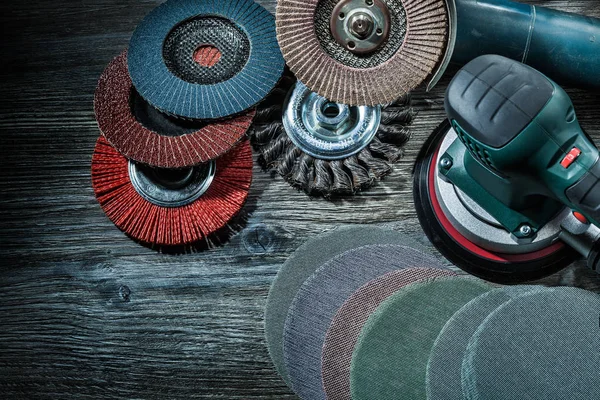
Selecting the correct abrasive material is essential for ensuring that your project meets its desired specifications. The right choice can improve efficiency, reduce costs, and enhance the quality of your work. At M/s Sandpaper Rodiez, we understand the importance of choosing abrasives tailored to your specific needs. Here’s a comprehensive guide to help you make the best abrasive material selection for your project.
1. Understanding the Basics of Abrasives
What are Abrasives?
Abrasives are materials used to wear away, polish, or clean the surface of another material through friction. They come in various forms, including sandpaper, grinding wheels, and blasting media.
Types of Abrasives:
- Natural Abrasives: Includes materials like garnet and emery, derived from natural mineral sources.
- Synthetic Abrasives: Engineered for specific properties, such as aluminum oxide, silicon carbide, and diamond.
Key Factors to Consider:
- Material hardness
- Grit size
- Shape and form
- Cost and availability
2. Identifying Your Project Requirements
Assessing the Material to be Worked On
- Metal: Requires hard abrasives like aluminum oxide or silicon carbide.
- Wood: Needs softer abrasives, such as garnet or aluminum oxide.
- Glass/Ceramics: Demands precision abrasives like diamond or silicon carbide.
Determining the Desired Finish
- Rough Finish: Coarser grit abrasives like steel grit.
- Smooth Finish: Finer grit abrasives like emery or garnet.
Considering the Project Scale
- Small Projects: Hand tools and sandpaper with medium to fine grits.
- Large-Scale Operations: Industrial abrasives like grinding wheels and blasting media.
Environmental and Safety Considerations
- Eco-Friendly Options: Garnet and pumice.
- Safety Requirements: Non-toxic and low-dust generating materials.
3. Exploring Different Abrasive Materials
Aluminum Oxide
- Best For: Metalworking, woodworking
- Advantages: Durable, versatile, available in various grits
- Drawbacks: May not be suitable for softer materials
Silicon Carbide
- Best For: Hard materials like glass and ceramics
- Advantages: Sharp cutting action, can be used wet or dry
- Drawbacks: Brittle, shorter lifespan
Ceramic Alumina
- Best For: Heavy-duty grinding, aerospace and automotive industries
- Advantages: Self-sharpening, cool cutting action
- Drawbacks: Higher cost compared to other abrasives
Garnet
- Best For: Sandblasting, wood finishing
- Advantages: Environmentally friendly, recyclable
- Drawbacks: Limited to specific applications
Diamond Abrasives
- Best For: Precision cutting, grinding hard materials
- Advantages: Hardest material, precise and efficient
- Drawbacks: High cost, specialized use
Cubic Boron Nitride (CBN)
- Best For: Machining hard metals
- Advantages: Heat-resistant, long-lasting
- Drawbacks: Limited to ferrous metals
4. Choosing the Right Grit Size
Understanding Grit Size
- Coarse Grit (40-60): Removes material quickly, ideal for rough shaping.
- Medium Grit (80-120): Balances material removal and surface finish.
- Fine Grit (150-240): Used for finishing, preparing surfaces for painting or coating.
- Very Fine Grit (320 and above): Polishing and finishing delicate surfaces.
Matching Grit Size to Your Project
- Initial Shaping: Coarse grit for rapid material removal.
- Intermediate Smoothing: Medium grit for preparing the surface.
- Final Finishing: Fine or very fine grit for achieving a smooth finish.
5. Considering Abrasive Form and Application
Coated Abrasives (Sandpaper)
- Best For: Hand sanding, light-duty machine sanding
- Applications: Woodworking, metalworking, paint removal
- Tips: Choose the right backing material (cloth, paper) for durability.
Bonded Abrasives (Grinding Wheels)
- Best For: Heavy-duty grinding, material shaping
- Applications: Metal fabrication, cutting tools
- Tips: Select the right bond type (vitrified, resin) based on the material being worked on.
Loose Abrasives (Blasting Media)
- Best For: Surface preparation, cleaning
- Applications: Automotive, construction, marine
- Tips: Ensure compatibility with your blasting equipment and material.
Non-Woven Abrasives (Scouring Pads)
- Best For: Surface conditioning, cleaning
- Applications: Polishing, blending, deburring
- Tips: Choose the appropriate grade (coarse, medium, fine) for the task.
6. Evaluating Cost vs. Performance
Cost Considerations
- Budget-Friendly Options: Aluminum oxide, garnet
- High-Performance Options: Ceramic alumina, diamond, CBN
Performance Metrics
- Durability: Longer-lasting abrasives may cost more upfront but save money in the long run.
- Efficiency: Higher-quality abrasives can reduce processing time and improve quality.
Balancing Cost and Performance
- For Frequent Use: Invest in high-performance abrasives for better results and longevity.
- For Occasional Use: Opt for budget-friendly options that still meet your project’s needs.
7. Environmental and Safety Considerations
Eco-Friendly Abrasives
- Garnet: Recyclable and low-dust, ideal for environmentally conscious projects.
- Pumice: Natural, non-toxic, and gentle on surfaces.
Safety Considerations
- Dust Control: Choose abrasives that generate less dust or use wet sanding techniques.
- Toxicity: Avoid abrasives with harmful chemicals or heavy metals.
Implementing Safe Practices
- Use appropriate personal protective equipment (PPE) like masks, goggles, and gloves.
- Ensure proper ventilation when working with abrasives that generate dust.
8. Tips for Optimal Abrasive Use
Preparation
- Clean the work surface to ensure effective abrasion.
- Choose the right tool for applying the abrasive, whether hand tools or power tools.
Application
- Apply even pressure to avoid uneven wear and tear on the abrasive.
- Use a consistent speed when working with power tools.
Maintenance
- Store abrasives in a dry, cool place to prevent degradation.
- Regularly check and replace worn-out abrasives to maintain efficiency.
9. Common Mistakes to Avoid
Overlooking Material Compatibility
- Ensure the abrasive is suitable for the material you’re working on to avoid damage or poor results.
Using the Wrong Grit Size
- Don’t start with too fine a grit for rough work, as it will be less effective and wear out quickly.
Neglecting Safety Precautions
- Always wear the necessary PPE and follow safety guidelines to prevent injuries.
10. Making the Final Decision
Consulting with Experts
- Contact M/s Sandpaper Rodiez for personalized advice and recommendations on the best abrasive material for your project.
Testing Abrasives
- If possible, test a small quantity of the chosen abrasive to ensure it meets your project’s requirements.
Investing in Quality
- Choose high-quality abrasives to achieve better results and longer-lasting performance.
Conclusion
Choosing the right abrasive material for your project is a critical step that can significantly impact the outcome. By understanding your project’s specific needs and the characteristics of various abrasives, you can make informed decisions that enhance efficiency, quality, and safety. M/s Sandpaper Rodiez is committed to helping you find the perfect abrasive solution tailored to your project requirements. Visit our website or contact us for expert guidance and top-quality abrasives.